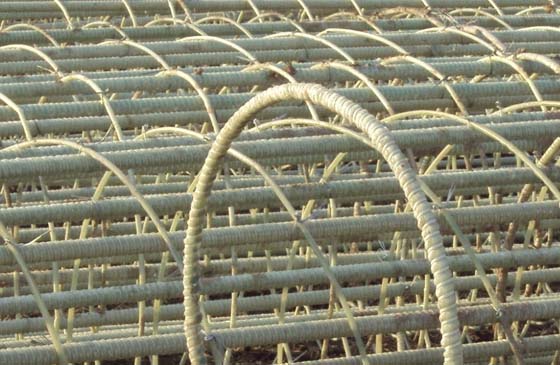
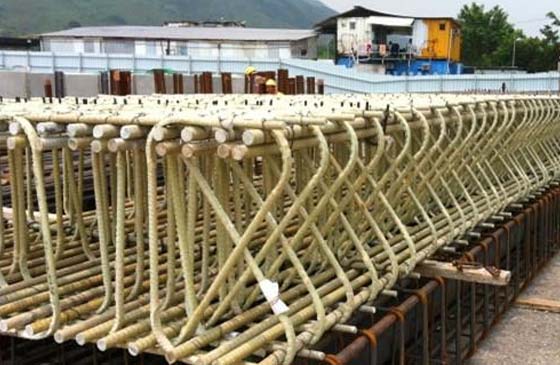
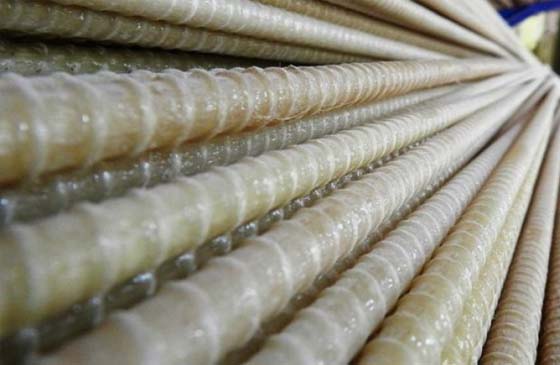
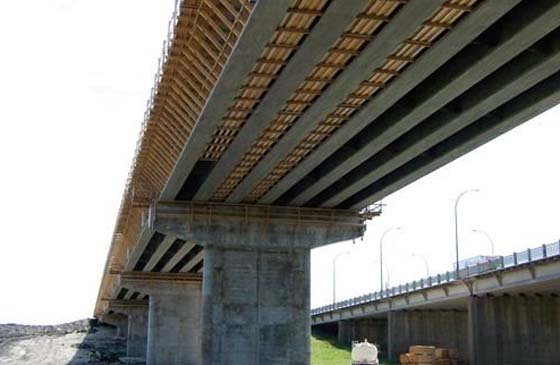
Introduction
GSL is the distributer of FRP nanocomposite rebar production with epoxy resin in Turkey, which relies on the extensive science of nano-polymers and nano-composites, as well as technical, engineering and structural knowledge and information, and the use of advanced machinery and serious monitoring of product quality, has always focused on innovation in production of requirements of a wide range of customers and dependence on foreign producing countries and so reduce the final price of the product.
Why composite rebar?
As we are aware, concrete inherently has the strength to withstand compressive forces, but tensile forces cause concrete to break. To strengthen concrete and heavy structures, rebars are used in concrete to strengthen against tensile forces, the final steel rebars have been 1968 structure of which is called reinforced concrete. Since used to increase the tensile strength of concrete. Despite their unique functional characteristics, steel rebars are severely exposed to harsh environments. conditions, i.e., high humidity, very cold or hot environments, alkaline and acidic conditions related to salts in the air etc. and hence they are highly susceptible to damage caused by corrosion and as a result reduce the life of structures and destroy them. Another major problem of steel rebars is their high weight compared to their strength. High weight of rebars cause dead loads in the structure. Therefore, researchers looked in to the use of FRP and produced different models of FRP rebars and composite rebars, which lead to very favorable results to the extent that today many structures are made using composite rebars worldwide.
The most commonly used types of composite rebars are: composite rebars with carbon fibers (CFRP), composite rebars with glass fibers (GFRP) and composite rebars with basalt fibers (BFRP), among which composite rebars made with glass fibers are both the cheapest the most common available worldwide, which itself has different resin coatings (epoxy, polyester and vinyl ester resins) among which the 3 best properties and applications are that of epoxy resins, then vinyl ester and last polyester.
The price and properties a user receive from GFRP composite rebars is very suitable compared to steel rebars because if a user wants the same properties from steel rebar, he must pay several times more than the price of GFRP rebar. These rebars significantly prevent losses caused by steel rebar corrosion in corrosive and acidic environments. Use of GFRP rebar is the best option for reinforcing concrete in places where there is a need for lack of proximity with electric and magnetic fields. FRP rebars can also be used to design and build new buildings.
With the properties it has, reduces the diameter and increases the distance of rebars in reinforced concrete items such as slabs, tunnels, foundations, etc. Also, FRP reinforcement increases the damping created in the structure against vibrations caused by earthquakes or industrialized equipment, and they are the best option to increase the structure’s resistance against earthquakes or vibrations and strengthening with FRP.
Properties of composite rebars
Corrosion resistance
Undoubtedly, the most prominent and essential feature of FRP composite products is their resistance against corrosion, which is why they are the best choice as a substitute for steel rebar. The life of FRP composite rebars is 15 times longer compared to steel rebars due to their very high corrosion resistance.
Electrical and magnetic insulation
Since these materials are made from a combination of resin and carbon glass fibers or aramid, no stress caused by magnetic field is introduced into them. Due to this feature in FRP composite materials, it is recommended to use FRP rebars in structures affected by electromagnetic fields such as reactors, airports, hospital MRI departments and laboratories. Electrical conductivity in the structure can be considered a risk. Electrical conductivity in metals is a dangerous issue and can cause damage. In contrast to metals, FRP composite materials are electrically non-conductive, which makes them a suitable choice for structures exposed to electric field.
Very low weight of FRP composite rebars
Rebars with a specific weight of 2.2 grams per cubic centimeter are much lighter than common steel bars with a specific weight of 7.85. This reduction in density can lead to a reduction in cost of transportation and facility in movement, as well as reduction in the dead load of the structure.
Resistance to fatigue
FRP composites are more resistant to alternating loading cycles (fatigue) than steel rebars, so they are widely used in the aerospace industry.
Economic savings
The price of this product is about %25 lower than its steel type; the important points of which are mentioned below:
Tensile strength
The tensile strength of composite rebars is 3 times higher than the strength of steel rebars.
A3 steel rebars have a tensile strength of 480 MPa iMPa at best, but composite rebars with glass fibers (GFRP) have a tensile strength of 1600 MPa. When an FRP reinforced composite rebar is subjected to tensile loading, no plastic behavior is observed in the sample until the yield point is reached. The tensile behavior of FRP rebars is affected by the type of fibers and is proportional to their stress-strain behavior until the moment of rupture.
The hardness and tensile strength of FRP rebars depend on several factors. Since in FRP rebars, the strength is basically carried out by the reinforcing fibers, the type and volume fraction of the fibers used and most importantly the orientation of the fibers strongly affects the tensile properties of FRP rebars.
Application of GFRP composite rebars
- Sewage facilities such as treatment plants, clarifiers, manholes, grease traps
- Concrete channels and pipes for conducting sewage and industrial effluents and chemicals.
- Concrete structures of docks and marine structures
- Structures adjacent to MRI machines in healthcare centers
- Reinforcement in the deck of bridges in cold regions and reinforced concrete substructures
- Concrete walls inside subway tunnels
- Nailing and soil consolidation
- Candles in soil and water
- Open channels and concrete pipes for conducting water.
- New Jersey prefabricated road concrete blocks
- Prefabricated concrete buildings.
- Prefabricated facade panels (GRC)
- Prefabricated walls, columns and prefabricated foundation for wall covering and landscaping.
- Power poles and replacement poles of power transmission towers
- Prefabricated concrete substation room.
- Floor reinforcement of parking lots and industrial halls
- Concrete dropped floor and ceiling.
- Making well screens
- Concrete dams
- Train tracks traverses
- Foundations
- TBM well
- Ceilings
- Tanks
- Use on wharf decks and shipping ports.
- Retaining walls
- Breakwater and marine platforms
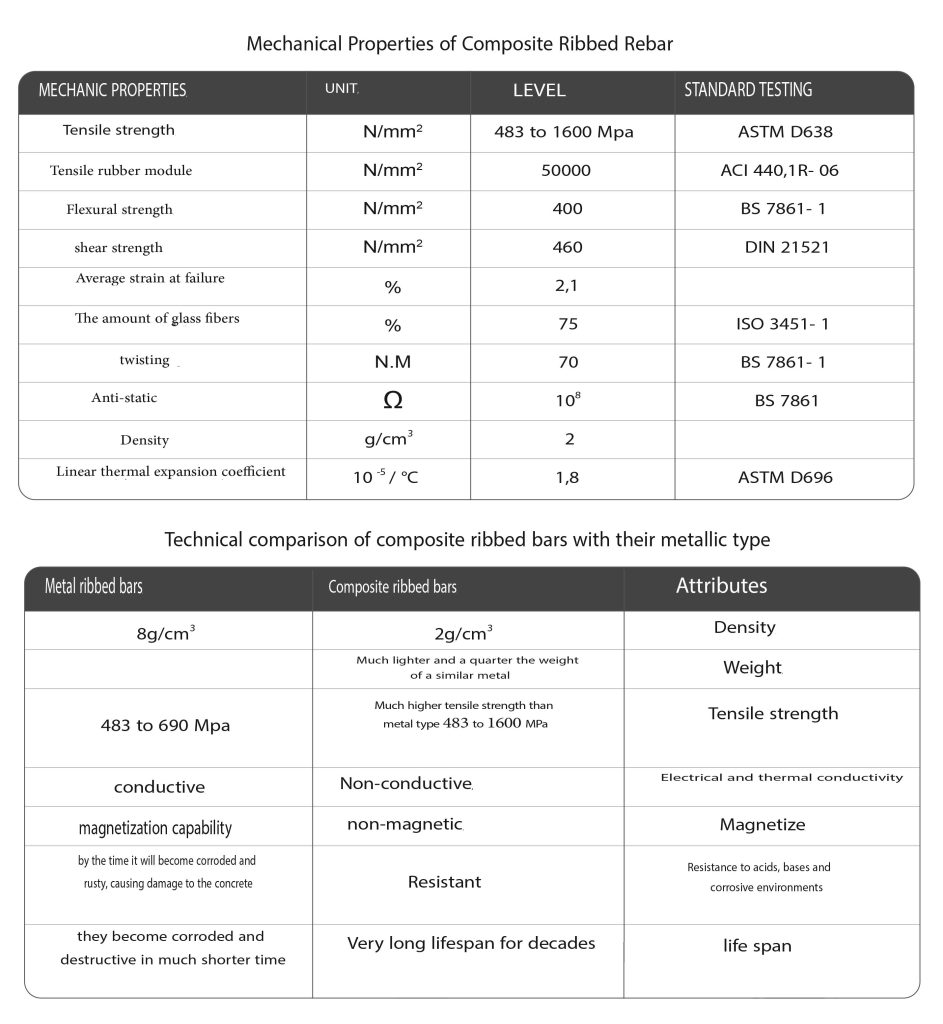
Tensile test
According to: ISO 10406-1:2015 and sent instruction.
Results of tensile test:
No. | Diameter (mm) | Initial Area (mm2) | Gauge length (mm) | Speed (mm/min) | Max. Force (N) | Elongation (%) | Tensile Strength@ Break (MPa) |
1 | 6.74 | 35.68 | 100 | 8 | 47381.38 | 3 | 1328 |
Notes
The specimens were prepared by the customer and prior to testing they were conditioned at standard laboratory conditions (23±2°C and 50+5% relative humidity) for 24 hours.
According to the standard, at least 3 specimens shall be tested.
Due to customer’s demand 2 specimens were tested.
Date of test: 28.07.2020