we produce various filter medias with different industrial applications and supply them to various industries. The manufactured goods are classified into different groups based on their applications, as well as raw materials, production processes and finishing operations, surface modifications, chemical operations, and other supplementary operations performed on them. According to their specific usage environment, regarding the size of the suspended particles and ambient temperature, as well as the amount of air passing through the filter surface and the desired efficiency level, different raw materials used in production of the filters. Synthetic fibers are the most important raw material in this production line, which in turn includes a wide range of fibers.
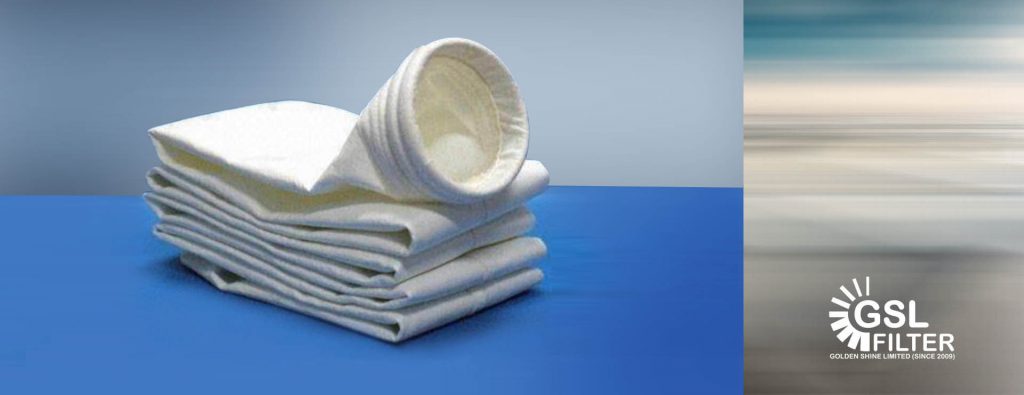
Fiber & materials used
According to their specific usage environment, regarding the size of the suspended particles and ambient temperature, as well as the amount of air passing through the filter surface and the desired efficiency level, different raw materials used in production of the filters. Synthetic fibers are the most important raw material in this production line, which in turn includes a wide range of fibers. These fibers used in production of non-textured layers of filters and they are used for improving the physical properties and mechanical strength of the final products in the surface layer (screen) of the filters. The most commonly used fibers in this production line are:
Polyester (PES)
Nylon (NY)
Polypropylene (PP)
Aramide Adjectives (M_Acrylic)
Graphite Fibers
Metal fibers
Polyacrylonitrile (PAN)
Anti-Static Fibers
Polyimid fibers (PPS)
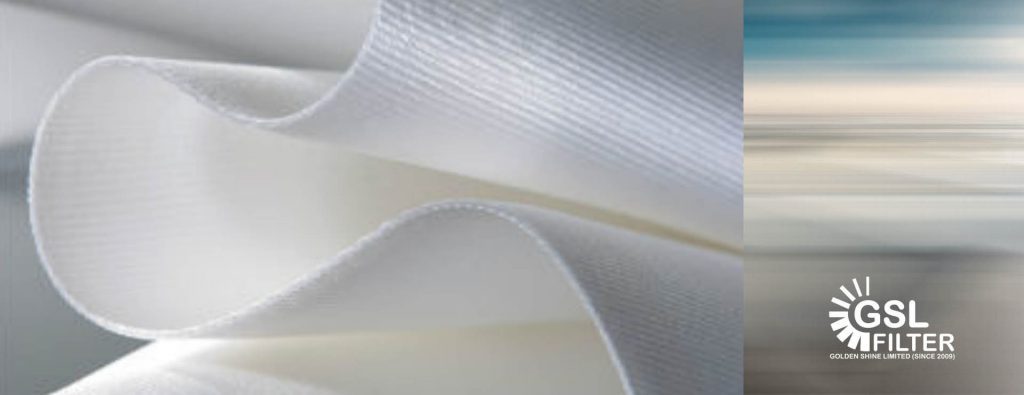
Supplemental and superficial modification in the filter media
Considering the divers applications of filter media and also features of infected environment in terms of the chemicals, temperature, humidity as well as type of particles in the air, variety of finishing processes have been done on filter media and filter bag. For correct selection and using a filter bag suitable for the environment, the trained staff and equipped laboratories of company have provided the possibility of making the right choice for users and enabling them to propose a cost-effective way ensuring a long life cycle and better efficiency.
Finishing operations on the filter media:
-Additional operations increase thermal power and resistance to flame and ignited particles in the environment -Anti-oil finishing -Waterproofing -Dust contamination finishing in order to prevent dust absorption and dirt (in proportion to the type of ambient particles) -Decrease in static electricity -Thermal stabilization and increased physical and mechanical resistance -Surface finish to reduce particle adhesion -Calendaring operations -Impregnation with Teflon materials and other chemicals to improve chemical resistance and physical properties
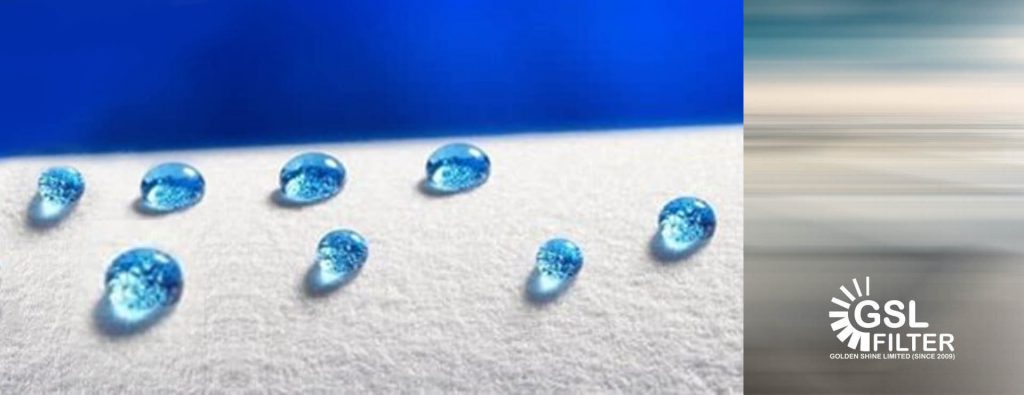
Resistance specifics of the fibers used:
The fibers used in the production of filter medias are categorized in four main groups based on the fibers thermal resistance and structure type of the constitutive polymer of fiber molecular chains:
Fibers used at ambient temperature: These fibers are usable at temperatures below 60 celsius degrees.
1-Fibers Used at Average Temperature: This group of fibers, which are one of the most popular gas and liquid phase filters, are used at temperatures up to 130 celsius degrees .
2-Fibers used at high temperatures: These fibers withstand up to 200 celsius degrees and can be used in the filter media structure.
3-Fibers used at extremely high temperatures: For temperatures higher than 200 celsius degrees, this group of fibers is used. These fibers have highly resistant molecular and polymer structures, which can be used to produce highly resistant filters.
In addition to the thermal resistance of the fibers used in the media filter structure, we should also consider other chemical and physical properties of the fibers, such as air permeability, resistance to acidic and alkaline environments, abrasion resistance, tensile strength, fracture resistance, resistance to de-lamination effect, hydrolysis, oxidation, resistance to moist environments, reaction to solvents, molten metal chips and many other mechanical, physical and chemical properties.
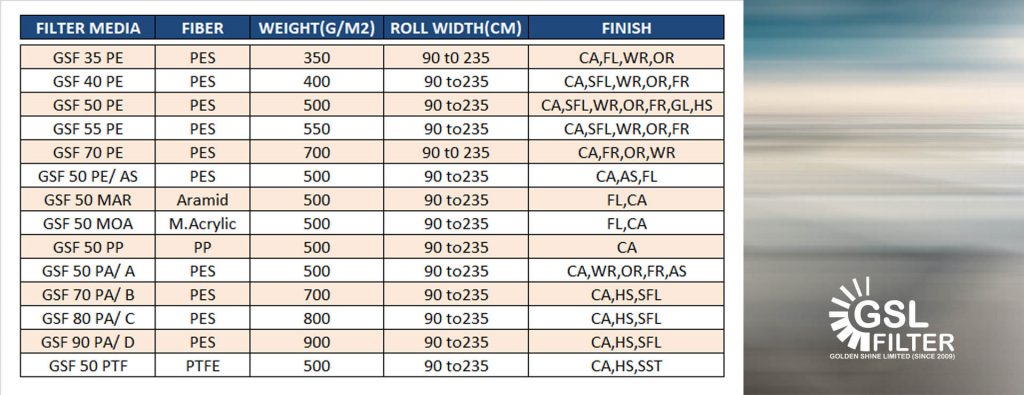
CA: Calendared
SFL: Soft surface treatment
SST: Soft surface treatment2
FL: Signed
GL: Glazed
OR: Oil repellent
WR: Water repellent
FR: Flame retardant
SL: Soil repellent
AS: Anti static
HS: Heat set
DS: Dimension stability
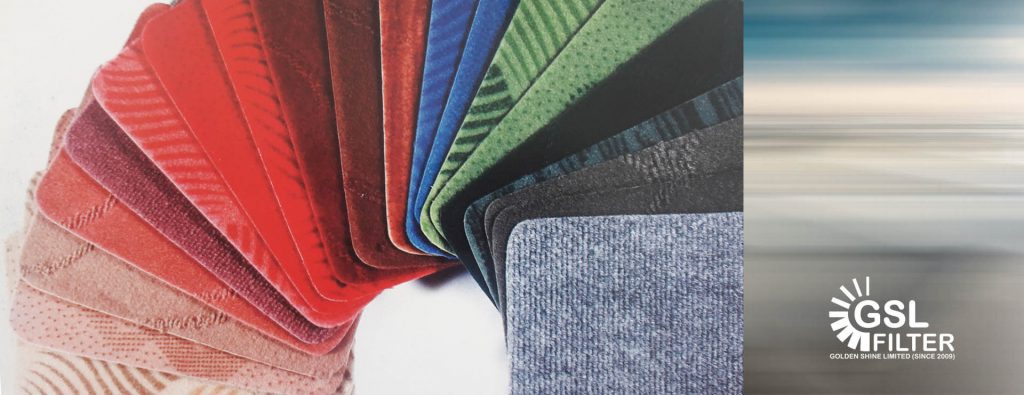